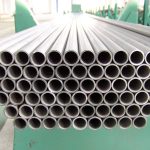
Süper paslanmaz çelik nedir? Nikel bazlı alaşım?
Şubat 18, 2025Asya-Pasifik
Şubat 27, 2025Kaplama ve Kaplama Arasındaki Fark Nedir??
Kaplama ve kaplama, endüstriyel bağlamlarda sıklıkla birbirinin yerine kullanılan terimlerdir, Ancak uygulamaya bağlı olarak farklı anlamları vardır. Her iki işlem de, özelliklerini geliştirmek için bir alt tabaka üzerine bir malzeme tabakası uygulamayı içerir, gibi korozyon direnç, aşınma direnci, veya yapısal bütünlük. ancak, Onların yöntemleri, amaçlar, ve sonuçlar farklıdır.
Kaplama tipik olarak, kalın bir malzeme tabakasının bulunduğu daha geniş bir işlemi ifade eder. (genellikle metal, ama bazen polimerler veya seramikler) koruma sağlamak veya işlevselliği geliştirmek için bir temel malzemeye bağlanır. Kaplama tabakası genellikle rulo yapıştırma gibi teknikler kullanılarak uygulanır, patlayıcı yapıştırma, veya kaynak, Ve bir kaplamadan önemli ölçüde daha kalın olabilir - bazen milimetre ile santimetre arasında değişir. Kaplama genellikle, kaplamanın yapının ayrılmaz bir parçası haline geldiği kompozit bir malzeme oluşturmak için kullanılır, hem korumaya hem de mekanik dayanıma katkıda bulunur.
Kaplama, Gel gelelim, tipik olarak bir alt tabakanın yüzeyine uygulanan daha ince bir malzeme tabakasını tanımlayan daha spesifik bir terimdir, genellikle kaynak veya termal püskürtme yoluyla. Bir kaplamanın birincil amacı, aşınmaya karşı direnç gibi yüzey özelliklerini geliştirmektir, korozyon, veya ısı—alt tabakanın yığın özelliklerini önemli ölçüde değiştirmeden. Kaynak kaplaması, Kaplamanın bir alt kümesi, kaynak teknikleri ile bir metal tabakanın biriktirilmesini içerir, dayanıklı ve metalurjik olarak bağlı bir çözüm haline getirir.
İşte kısa bir karşılaştırma:
Yüz
|
Kaplama
|
Kaplama
|
---|---|---|
Kalınlığı
|
Daha kalın (milimetre ila santimetre)
|
Tiner (mikron ila birkaç milimetre)
|
Amaç
|
Yapısal iyileştirme, koruma
|
Yüzey özelliği geliştirme
|
Yapıştırma
|
Mekanik veya metalurjik
|
Tipik olarak metalurji (Örneğin., Kaynak)
|
Yöntemler
|
Rulo bağı, patlayıcı yapıştırma, Kaynak
|
Kaynak, termal püskürtme
|
Malzeme Değişimi
|
Genellikle toplu özellikleri değiştirir
|
Öncelikle yüzeyi etkiler
|
Pratikte, ayrım bulanık olabilir, Özellikle “kaplama” ve “kaplama” nın kaynaklardan ayrılmış katmanlara atıfta bulunabileceği kaynak bağlamlarında. ancak, Kaplama daha önemli bir katman ima etme eğilimindedir, Kaplama yüzey seviyesi iyileştirmelere odaklanırken.
Kaynak kaplaması nedir?
Kaynak kaplaması, Kaynak kaplama veya sert yüzey olarak da bilinir (Bağlama bağlı olarak), bir taban malzemesine biriken bir metal tabakası bırakıldığı bir işlemdir (alt tabaka) Kaynak tekniklerini kullanma. Bu katman, Overlay olarak adlandırılır, metalurjik olarak substrata bağlanır, yani iki malzeme moleküler düzeyde kaynaşır, Güçlü Bir Yaratmak, dayanıklı bağlantı. Kaynak kaplamasının amacı, substratın yüzey özelliklerini iyileştirmektir - korozyona karşı direnç gibi, erozyon, aşınma, veya yüksek sıcaklıklar - tüm bileşeni değiştirmeden.
Kaynak kaplaması, sert ortamlara maruz kalan bileşenlerin servis ömrünü uzatmak için yaygın olarak kullanılır. Örneğin, Bir çelik boru, asidik sıvıları işlemek için korozyona dayanıklı alaşım kaplama alabilir, veya bir araç, aşınmaya dayanacak sert bir kaplama alabilir. Daha ucuz bir taban malzemesinin kullanılmasına izin verdiği için süreç uygun maliyetlidir. (Örneğin., karbon çelik) sadece gerektiğinde premium bir malzeme uygularken.
Kaynak kaplama işlemi, bir dolgu malzemesinin eritilmesini içerir (tel, çubuk, veya toz) Isı kaynağı kullanmak (Örneğin., Ark, plazma, veya lazer) ve substrata yatırmak. Overlay malzemesi istenen özelliklere göre seçilir, ve substrat tipik olarak termal stresi en aza indirmek ve uygun bağlamayı sağlamak için önceden ısıtılır.
Kaynak kaplama işlemleri türleri
Birkaç kaynak kaplama işlemi var, her biri uygulamaya bağlı olarak benzersiz avantajlara sahip, malzeme, ve hassasiyet gerekli. Aşağıda en yaygın türler, ardından temel ayrıntıları özetleyen bir tablo.
-
Korumalı Metal Ark Kaynağı (SMAW)
-
Çubuk kaynağı olarak da bilinir, Smaw, akı ile kaplanmış bir sarf malzemesi elektrot kullanır. Basit, taşınabilir, ve uygun maliyetli ancak biriktirme üzerinde sınırlı kontrol sunar ve geniş alanlar için daha yavaştır.
-
-
Gaz metal ark kaynağı (GMAW)
-
MIG kaynağı olarak bilinir, Gmaw, sürekli bir tel elektrot ve korumalı bir gaz kullanır. Smaw'dan daha hızlı ve otomatik sistemler için uygun, Temiz bir ortam gerektirse de.
-
-
Gaz Tungsten Ark Kaynağı (GTAW)
-
Tig kaynağı denir, GTAW, tüketilmeyen bir tungsten elektrot ve ayrı bir dolgu malzemesi kullanır. Yüksek hassasiyet ve kalite sağlar, İnce kaplamalar veya kritik uygulamalar için ideal, Ama daha yavaş ve daha pahalı.
-
-
Plazma aktarılan ark kaynağı (PTW)
-
PTAW, toz dolgu malzemesini eritmek için bir plazma ark kullanır, Kaplama kalınlığı ve minimal seyreltme üzerinde mükemmel kontrol sunan (substrat ile karıştırmak). Sabit ve korozyona dayanıklı bindirmeler için yaygın olarak kullanılır.
-
-
Tozaltı Ark Kaynağı (GÖRDÜM)
-
Testere, kaynağı koruyan bir akı tabakasına gömülü sürekli bir tel elektrot içerir. Büyük için son derece verimli, Kalın kaplamalar ancak karmaşık şekiller için daha az çok yönlü.
-
-
Lazer kaynak kaplaması (Lazer kaplama)
-
Bu gelişmiş yöntem, bir dolgu malzemesini eritmek için bir lazer kullanır (toz veya tel) substrat üzerine. Hassasiyet sunar, Düşük ısı girişi, ve minimal bozulma, yüksek değerli bileşenler için ideal.
-
-
Oksi-yakıt kaynağı (OFW)
-
Overlay için daha az yaygın bir yöntem, OFW, dolgu maddesini eritmek için bir alev kullanır. Basittir ancak hassasiyetten yoksundur ve nadiren modern endüstriyel kaplamalar için kullanılır.
-
İşte bu işlemleri karşılaştıran bir tablo:
İşlem
|
Isı kaynağı
|
Dolgu türü
|
Kesinlik
|
Hız
|
Tipik kullanım
|
---|---|---|---|---|---|
SMAW
|
Elektrikli ark
|
Çubuk elektrot
|
Düşük
|
Yavaş
|
Genel onarım, küçük alanlar
|
GMAW
|
Elektrikli ark
|
Tel
|
Orta
|
Ilıman
|
Otomatik kaplamalar, orta ölçek
|
GTAW
|
Elektrikli ark
|
Çubuk/tel
|
Yüksek
|
Yavaş
|
Kesinlik, İnce bindirmeler
|
PTW
|
Plazma ark
|
Toz
|
Yüksek
|
Ilıman
|
Sert, Kritik bileşenler
|
GÖRDÜM
|
Elektrikli ark
|
Tel
|
Orta
|
Hızlı
|
Kalın kaplamalar, Büyük yüzeyler
|
Lazer kaynağı
|
Lazer ışını
|
Toz/Tel
|
Çok yüksek
|
Ilıman
|
Yüksek değerli, kesin uygulamalar
|
OFW
|
Oksi-yakıt alev
|
çubuk
|
Düşük
|
Yavaş
|
Temel, Düşük teknoloji kaplamaları
|
Her süreç, maliyet gibi faktörlere göre farklı ihtiyaçlara uygun, bileşen boyutu, ve performans gereksinimleri.
Lazer Kaynak Kaplama İşlem Avantajları
Lazer kaynak kaplaması, Lazer kaplama olarak da bilinir, Gelişmiş yetenekleri için öne çıkıyor. Bir dolgu malzemesini eritmek için odaklanmış bir lazer ışını kullanır (tipik olarak toz veya tel) ve alt tabakaya yatırın. Süreç oldukça kontrollüdür, çeşitli faydalarla sonuçlanır:
-
Hassasiyet ve kontrol
-
Lazer ışını ince ayarlanabilir, İnce izin vermek, üniforma kaplamaları (kadar küçük 0.1 mm) ve karmaşık desenler. Bu, küçük alanları onarmak veya karmaşık geometrilere kaplama uygulamak için idealdir..
-
-
Düşük ısı girişi
-
Geleneksel kaynaktan farklı olarak, Lazer kaplama ısıya etkilenen bölgeyi en aza indirir (YAPMAK), substratta termal bozulma ve stresi azaltmak. Bu, temel malzemenin özelliklerini korur.
-
-
Minimal seyreltme
-
Overlay malzemesi, alt tabaka ile daha az karışır, Uygulanan katmanın amaçlanan özelliklerini korumasını sağlamak (Örneğin., korozyon direnci veya sertlik).
-
-
Yüksek bağlanma mukavemeti
-
Metalurjik bağ güçlü ve kusursuz, Hızlı soğutma oranları ve hassas enerji iletimi sayesinde.
-
-
Çok yönlülük
-
Lazer kaplama çok çeşitli malzemelerle çalışır, Metaller dahil, alaşımlar, Ve hatta seramikler, ve tutarlılık için otomatikleştirilebilir.
-
-
Azaltılmış malzeme atığı
-
Odaklanmış uygulama sadece gerekli miktarda dolgu kullanır, Titanyum veya nikel alaşımları gibi pahalı malzemeler için verimli ve uygun maliyetli hale getirme.
-
-
Geliştirilmiş yüzey kalitesi
-
Overlay, pürüzsüz yüzeyi ve gözeneklilik veya çatlak eksikliği nedeniyle genellikle çok az işlem gerektirir veya hiç işlem gerektirmez..
-
-
Çevresel Faydalar
-
Düşük enerji tüketimi ve sarf malzemelerine duyulan ihtiyaç (Örneğin., Koruyucu Gazlar) Bazı geleneksel yöntemlerden daha sürdürülebilir hale getirin.
-
Bu avantajlar, kalite ve uzun ömürlülüğün kritik olduğu yüksek teknolojili endüstriler için lazer kaynak kaplamasını tercih edilen bir seçim haline getirir.
Endüstriler ve uygulamalar
Kaynak kaplaması, lazer kaplama dahil, bileşen performansını ve uzun ömürlülüğü artırmak için çok sayıda sektörde kullanılmaktadır. Aşağıda kilit endüstriler ve uygulamaları, Örnekleri özetleyen bir tablo ile.
-
Yağ ve gaz
-
Boru hattı, valfler, ve bağlantı parçaları korozyona dayanıklı kaplamalar alır (Örneğin., İnkonel) Sert sıvılara ve yüksek basınçlara dayanmak için.
-
-
Enerji üretimi
-
Türbinli bıçaklar, Kazan tüpler, ve ısı eşanjörleri aşınmaya direnmek için kaplamalar kullanır, sıcaklık, ve oksidasyon.
-
-
Havacılık
-
Motor bileşenleri ve yapısal parçalar dayanıklılık ve hafif performans için kaplamalar alır, genellikle titanyum veya nikel alaşımları kullanılarak.
-
-
Madencilik
-
Ekskavatör kovaları, kırıcı rulolar, ve matkap bitleri, kayalardan ve minerallerden aşınmaya direnmek için serttir..
-
-
Otomotiv
-
Motor vanaları, dişliler, ve kalıplar aşınma direncini artırmak ve hizmet ömrünü uzatmak için kaplamalar alır.
-
-
Kimyasal İşleme
-
Reaktörler, pompalar, ve boru sistemleri, agresif kimyasalları işlemek için korozyona dayanıklı kaplamalar kullanır.
-
-
İmalat
-
Kesme aletleri, kalıplar, ve kalıplar keskinliği korumak ve tekrarlayan strese dayanmak için kaplanmıştır.
-
Sanayi
|
Uygulama
|
Kaplama amaç
|
---|---|---|
Yağ ve gaz
|
Boru hattı, valfler
|
Korozyon ve basınç direnci
|
Enerji üretimi
|
Türbinli bıçaklar, kazan borusu
|
Isı ve aşınma direnci
|
Havacılık
|
Motor parçaları, iniş takımı
|
Dayanıklılık, hafif güç
|
Madencilik
|
Kovalar, kırıcılar
|
Aşınma direnci
|
Otomotiv
|
Vanalar, dişliler
|
Aşınma direnci, uzun ömürlülük
|
Kimyasal İşleme
|
Pompalar, reaktörler
|
Korozyon direnci
|
İmalat
|
Aletler, kalıplar
|
Sertlik, kesinlik
|
Bu uygulamalar, kaynak kaplamasının bakım maliyetlerini ve kesinti sürelerini azaltmadaki rolünü vurgulamaktadır.
Genellikle kaynak kaplaması için kullanılan malzemeler
Yer paylaşımı malzemesinin seçimi, alt tabaka ve istenen özelliklere bağlıdır. Aşağıda yaygın olarak kullanılan malzemeler var, ardından örnek ve amaçlı bir tablo.
-
Paslanmaz çelik
-
Mükemmel korozyon direnci ve orta aşınma direnci sunar. Ortak notlar arasında 316L ve 308.
-
-
Nikel Esaslı Alaşımlar
-
Inconel gibi malzemeler 625 ve hastelloy korozyona karşı üstün direnç sağlar, sıcaklık, ve oksidasyon.
-
-
Kobalt bazlı alaşımlar
-
Stellite alaşımları (Örneğin., Stellit 6) sertlik ve aşınma direnci ile ünlüdür, Özellikle yüksek sıcaklıklarda.
-
-
Tungsten karbür
-
Aşırı aşınma direnci için sertleştirmede kullanılır, genellikle metal bir matrisle harmanlanır.
-
-
Krom karbür
-
Yüksek kısıtlı ortamlarda aşınma direnci için uygun maliyetli bir çözüm sağlar.
-
-
Titanyum Alaşımları
-
Hafif ve korozyona dayanıklı, Havacılık ve Deniz Uygulamalarında Kullanılır.
-
-
Bakır bazlı alaşımlar
-
Rulmanlar gibi belirli uygulamalarda termal iletkenlik ve aşınma direnci için uygulandı.
-
Malzeme
|
Anahtar Özellikler
|
Ortak uygulamalar
|
---|---|---|
Paslanmaz çelik
|
Korozyon direnci
|
Boru hattı, kimyasal reaktörler
|
Nikel Alaşımları
|
Sıcaklık, korozyon direnci
|
Türbinli bıçaklar, petrol teçhizatları
|
Kobalt alaşımları
|
Sertlik, aşınma direnci
|
Madencilik araçları, valfler
|
Tungsten karbür
|
Aşırı aşınma direnci
|
Matkap bitleri, kırıcılar
|
Krom karbür
|
Aşınma direnci
|
Konveyör sistemleri, plaka giymek
|
Titanyum Alaşımları
|
Hafif, korozyon
|
Havacılık bileşenleri
|
Bakır alaşımları
|
Isı iletkenliği
|
Yatakları, elektrik parçaları
|
Bu malzemeler, bileşenin karşılaştığı çevresel zorluklara uyacak şekilde seçilmiştir..
Daha derin bir anlayış sağlamak için, Her bölümü daha fazla keşfedelim.
Kaplama vs. Uygulamada kaplama
Gemi yapımı gibi sektörlerde, Kaplama, patlayıcı bağlanma kullanarak kalın bir paslanmaz çelik plakanın bir karbon çelik gövdesine yapıştırılmasını içerebilir, sağlam bir yaratmak, korozyona dayanıklı dış cepheye. Kaplama, ancak, Korozif deniz suyuna karşı korunmak için bir borunun içine ince bir nikel alaşımı kaynağını kaynaklamayı içerebilir. İkisi arasındaki seçim, hedefin yapısal takviye olup olmadığına bağlıdır (kaplama) veya yüzey geliştirme (kaplama). Bazı durumlarda, Kaynak bindirmesi bir tür kaplama olarak kabul edilir, Özellikle daha kalın katmanlar uygulandığında, terminolojideki örtüşmeyi göstermek.
Kaynak kaplama işlem detayları
Kaynak kaplama işlemi yüzey hazırlığı ile başlar - termal şoku azaltmak için substratı temizlemek ve bazen önceden ısıtmak. Kaynak yöntemi daha sonra katmanlar halinde kaplama malzemesini yatırır, her geçişte çatlaklar veya gözeneklilik gibi kusurlardan kaçınmak için dikkatlice kontrol edilir. WELD sonrası tedaviler, öğütme veya ısı işlemi gibi, yüzeyi iyileştirebilir veya stresleri hafifletebilir. Otomasyon giderek yaygınlaşıyor, özellikle lazer ve PTAW işlemleri ile, Tutarlılığı artırmak ve işçilik maliyetlerini azaltmak.
Derinlemeli lazer kaynak kaplaması
Lazer Cladding’in hassasiyeti, enerjiyi küçük bir alana odaklama yeteneğinden kaynaklanmaktadır - bazen 0.5 MM-Türbin Bıçakları veya Tıbbi İmplantlarda Mikro Terikarlara İzin Verme. İnce duvarlı bileşenler için düşük ısı girişi kritiktir, geleneksel kaynağın çarpışmaya neden olabileceği yer. İşlem de gradyan katmanları yatırabilir, bir malzemeden diğerine geçiş (Örneğin., çelikten nikele), substrat ve kaplama arasındaki uyumluluğun arttırılması.
Sektöre özgü örnekler
Petrol ve gazda, Inconel kaynak kaplaması 625 Karbon çelik valfinde ekşi gaza dayanabilir (H2S) maruziyet, Offshore teçhizatlarda pahalı yedeklerin önlenmesi. Madencilikte, Tungsten karbür kaplamaları, kırıcı çenelerde binlerce ton cevheri yıpranmadan katlandıklarından emin. Havacılık ve uzay uygulamaları genellikle titanyumun motor parçalarına lazer kaplamasını içerir, Ağırlık tasarruflarını dayanıklılıkla dengelemek.
Malzeme Seçimi Nüansları
Inconel gibi nikel alaşımları pahalıdır, ancak aşırı ortamlarda maliyetlerini haklı çıkarır, arızanın bir seçenek olmadığı nükleer reaktörler gibi. Kobalt alaşımları, daha zorken, kırılgan olabilir, Bu nedenle genellikle daha sert substratlar üzerinde ince tabakalarda uygulanırlar. Tungsten Carbide’nin olağanüstü sertliği süneklik pahasına gelir, statik aşınma yüzeyleri için ideal hale getirir, ancak darbe ağır uygulamalar için daha az.
Kaynak kaplaması, Geleneksel yöntemler veya gelişmiş lazer kaplama yoluyla olsun, malzeme performansını artırmak için çok yönlü ve temel bir tekniktir. Kaplamadan gelen ayrımı, yapısal değişimden ziyade yüzey iyileştirmesine odaklanıyor., Her ikisi de mühendislikte hayati rollere hizmet etse de. Bir dizi süreçle, Lazer kaplamaları gibi faydalar, ve madencilikten havacılığa sektörleri kapsayan uygulamalar, Kaynak kaplaması teknoloji ile gelişmeye devam ediyor. Seçilen Malzemeler - Düzensiz Çelik, nikel alaşımları, karbürler, ve daha fazlası - belirli zorlukların çözümü, dayanıklılık ve verimliliği sağlamak.