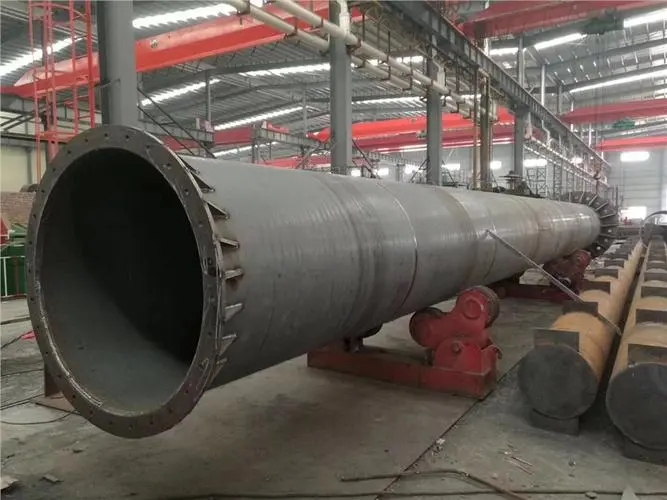
Sự mài mòn xảy ra như thế nào trong đường ống và tại sao thép chịu mài mòn cường độ cao hoạt động tốt hơn ống thép thông thường trong môi trường mài mòn
tháng sáu 21, 2022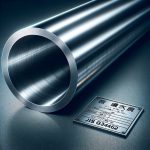
Kiến thức cơ bản và công dụng của ống thép liền khối, vỏ và ống dẫn dầu
tháng sáu 23, 2022Giảm số lượng biến thể, hoặc đạt được sự nhất quán về độ dày của tường hơn, có thể là sự khác biệt giữa việc đáp ứng các yêu cầu của khách hàng hay không. Nó cũng giúp giảm hoặc thậm chí có thể loại bỏ nhu cầu của khách hàng đối với các quy trình tiếp theo như gia công.
Ống liền mạch thường được sản xuất trên máy nghiền ống hai cuộn. Trong một số trường hợp, chỉ riêng bước này là đủ để sản xuất ống đáp ứng yêu cầu của khách hàng. Tuy nhiên, nếu độ dày của tường cần được cải thiện hơn nữa sau khi xuyên, một nhà sản xuất ống có thể sử dụng thiết bị bổ sung và các bước xử lý. Hai loại thiết bị như vậy là máy cán dài cán chéo (thường được biết đến với tên thương mại của nó, chẳng hạn như một nhà máy Assel hoặc một Diecher), và một băng ghế lạnh.
Tổng quan về ba bước quy trình
Sản xuất ống liền mạch thường bắt đầu bằng việc cán chéo nóng trong nhà máy đúc ống. Xỏ lỗ là bước quy trình đầu tiên để tạo ra ống có tường chất lượng cao. Bước này thường được theo sau bởi một hoặc nhiều quy trình kéo dài có thể cải thiện chất lượng thành đồng thời tăng chiều dài ống. Sau khi ống rời khỏi máy nghiền liền mạch và nguội, nó có thể được hoàn thành trên một băng ghế kéo lạnh như là bước thứ ba để cải thiện dung sai của tường.
Piercer Mill. Hầu hết sự chú ý về chất lượng tường liền mạch đều hướng vào máy nghiền ống. Sự chú ý này là hợp lý bởi vì máy nghiền khuyên có ảnh hưởng lớn nhất đến sự biến đổi của tường. Ống được sản xuất bởi một nhà máy xỏ lỗ có thể được tối ưu hóa để 7 đến 10 phần trăm tường biến thể.
Mặc dù một vỏ bị đâm thủng có thể có ít hơn 10 phần trăm tường biến thể, lượng biến thiên này là đối với phần tường tương đối dày. Ví dụ, đạt được dung sai thành ± 10 phần trăm tạo ra một ống có độ dày phạm vi thành 13.5 mm (0.531 trong.) đến 16.5 mm (0.650 trong.) trở lên khi đặt hàng tại 15 mm (0.590 trong.). Có thể cần phải xử lý thêm bằng máy nghiền kéo dài đối với các yêu cầu nghiêm ngặt hơn của khách hàng.
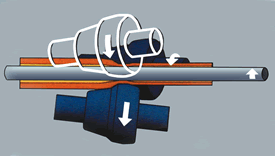
Quy trình cán chéo sử dụng ba cuộn làm việc để giảm OD của ống và độ dày thành ống. Bản vẽ của Copperweld, Shelby, Ohio.
Máy kéo dài. Năm loại máy kéo dài chính được sử dụng trong ngành công nghiệp sản xuất ống: nhà máy ống trục, băng ghế đẩy, nhà máy cắm điện, nhà máy giảm căng, và máy cán dài cán chéo. Năm mươi năm sử dụng trên toàn ngành đã cho thấy rằng, của những nhà máy kéo dài này, bộ kéo dài cán chéo cung cấp sự cải tiến đáng kể nhất về khả năng chịu đựng thành ống được sản xuất trên máy nghiền ống. Máy cán dài cán chéo sử dụng trục gia công trên OD và trục gá trên ID (Xem Nhân vật 1).
Ghế băng rút nguội. Vẽ trên băng ghế là một phương pháp hoàn thiện lạnh giúp cải thiện kích thước thành ống liền mạch. Trong quá trình vẽ băng ghế dự bị, đầu tiên ống được luồn một cách lỏng lẻo vào một trục gắn với một thanh. Sau đó, một cụm kìm kẹp chặt ống và kéo nó qua một cacbua cố định hoặc khuôn thép dụng cụ. Kết quả là một ống tùy chỉnh với khả năng kiểm soát kích thước rất tốt. Dung sai OD điển hình là ± 0,1 mm (± 0,004 in.), khoảng một phần mười khả năng chịu đựng của một ống liền mạch hoàn thiện nóng điển hình.
Các lợi ích bổ sung từ quá trình vẽ bao gồm nâng cao độ hoàn thiện bề mặt, khả năng cung cấp dung sai ID, và các đặc tính cơ học được cải thiện. ống được sản xuất bằng quy trình này yêu cầu xử lý tối thiểu hoặc bổ sung và được coi là sản phẩm có giá trị gia tăng.
Hướng dẫn về Độ giãn dài qua cuộn
Để kéo dài cán ngang, hai yêu cầu chính liên quan đến vỏ xuyên thủng. Chúng lấp đầy phần chiều cao của bướu để 80 đến 90 phần trăm thiết kế của nó và tối đa hóa độ bám bên đầu vào. Cả hai yêu cầu đều liên quan đến thiết kế cuộn chuyền trong nhà máy Assel.3
Nhân vật 2
Gù cuộn nằm gần giữa cuộn làm việc. Điều quan trọng là phải phù hợp với phần ống đi vào máy nghiền với các đặc điểm thiết kế của cuộn làm việc. Bản vẽ của Copperweld, Shelby, Ohio.
Làm đầy bướu. Gù là một thuật ngữ chung cho khu vực gần giữa cuộn công việc có chứa cấu hình nâng lên (Xem Nhân vật 2). Làm đầy bướu là vấn đề đo bức tường bị xuyên thủng và sau đó so sánh nó với kích thước bướu đã biết từ bản in. Máy nghiền kim loại sau đó được điều chỉnh để có được giá trị thích hợp. Ví dụ, nếu thiết kế bướu là 8 mm (0.315 trong.), vỏ bị xuyên thủng nên đo 7 mm (0.276 trong.) nhiều hơn quy mô khách hàng (tại vì 7 Là 90 phần trăm của 8).
Mối quan hệ này rất quan trọng trong sản xuất ống thành mỏng vì dung sai thành ống cơ học dựa trên tỷ lệ phần trăm (theo tiêu chuẩn ASTM A519). Khó đạt được dung sai đối với ống có thành mỏng hơn vì, ví dụ, 5 phần trăm của 5 mm (0.197 trong.) là một thứ nguyên chặt chẽ hơn nhiều so với 5 phần trăm của 10 mm (0.394 trong.). Các nhà sản xuất ống phải hiểu rằng nếu năng lực của nhà máy 1 mm (0.040 trong.) biến thể của tường, điều này có thể đại diện cho một nửa dung sai thương mại cho các phần tường trung bình (Giá trị Cp của 2.0) và sự thay đổi ngoài dung sai đối với các phần có thành mỏng (Cp nhỏ hơn 1.0).
Vỏ từ máy nghiền cần được giảm độ dày thành để đảm bảo lấp đầy chiều cao phù hợp. Đối với ống thành cực mỏng, các nhà sản xuất có thể nhận thấy rằng việc cải tiến chất lượng trong máy cán chéo có thể khó khăn nếu không muốn nói là không thể đạt được vì vỏ xuyên qua có quá nhiều thay đổi. Đối với một số kích thước ống, sự biến đổi thành phần trăm có thể tăng lên chứ không phải giảm trong máy nghiền ống. Tỷ lệ phần trăm của sự thay đổi được xác định bằng cách tính toán cẩn thận. Mặc dù tổng số chiều thay đổi làm giảm tử số, mẫu số giảm với tốc độ lớn hơn bởi vì ống từ máy kéo dài cán chéo có 50 đến 75 độ dày thành ít hơn phần trăm so với ống từ máy nghiền ống.
Cán chéo. Yêu cầu thứ hai là duy trì độ bám tốt nhất trong quá trình cán chéo. Grip được định nghĩa là số lượng đường xoắn ốc của ống trước đường tâm của bướu trong thiết kế cuộn cán của máy kéo dài cán chéo — nói một cách đơn giản, vỏ xuyên thủng nên tiếp xúc với mặt cuộn sớm trong quá trình để nguồn cấp dữ liệu ống được thiết lập trước khi nó gặp vùng làm việc trong phần gù. Công việc được thực hiện trong phần gù đòi hỏi rất nhiều năng lượng, lên đến vài nghìn mã lực. Lực lượng lao động được áp dụng trong một phần rất ngắn, thường xuyên 15 đến 25 mm (ít hơn 1 trong.) rộng. Nếu ống không được nắm chặt, nó sẽ quay hơn là cho ăn, hoặc nó có thể cấp dữ liệu không thường xuyên qua khu vực làm việc, tạo ra sự biến đổi.
Trong hầu hết các trường hợp, điều kiện tốt nhất cho vỏ xuyên qua đạt được bằng cách tạo ra đường kính bên ngoài tối đa phù hợp với mặt cuộn của máy cán dài cán chéo. Thông thường mối quan hệ này được giải quyết bằng cách điều chỉnh thiết lập máy nghiền ống để tạo ra kích thước ống chính xác. Nhưng trong một số trường hợp, có thể cần phải tăng hoặc giảm một chút góc phân kỳ của máy cán kéo dài để đảm bảo rằng vỏ sẽ vừa vặn và bám chặt..
Các thí nghiệm được tiến hành về chất lượng thành ống được lấy trực tiếp từ máy nghiền chất kéo dài được sử dụng để xác định xem các ống có chất lượng thành tốt hơn các ống được xử lý thêm bằng máy nghiền hồ hoặc máy nghiền giảm độ giãn hay không.. Người ta xác định rằng trong quá trình giảm kích thước, lực dọc và lực nén tác động lên tường và có thể làm tăng độ biến thiên của tường. Các ống được lấy trực tiếp từ máy cán dài cán chéo có độ dày thành ống vượt trội và chất lượng bề mặt tốt hơn vì chúng không tiếp xúc với các điều kiện cán trong máy nghiền hồ. Các ống đã qua nhà máy định cỡ, Tuy nhiên, có thể giảm bớt sự thay đổi của bức tường bằng cách vẽ nguội trên băng ghế dài.
Hướng dẫn Vẽ nguội
Thành công trong việc xử lý ống liền mạch kéo nguội phụ thuộc vào việc duy trì chất lượng thành ống cao từ máy nghiền nóng liền mạch và lựa chọn đúng các dụng cụ băng kéo lạnh (trục gá và bộ khuôn).
Ba điểm chính liên quan đến việc vẽ ống xuyên là:
- Cần giảm một số vách để đảm bảo trục gá cắn vào tường khi bắt đầu kéo và sau đó đặt trục gá đúng vào ổ trục trong quá trình kéo.. Nếu tường vào quá bất thường hoặc quá nhạt, trục gá sẽ không tiến vào ổ trục, và ống kết quả sẽ không có dung sai tốt đối với kích thước bên ngoài, kích thước bên trong, và độ dày tường.
- Bản vẽ băng ghế dự bị được giới hạn ở mức tối đa 40 giảm phần trăm diện tích. Nếu bức tường tới quá nặng, nó có thể làm cho kim loại bị hỏng thay vì tạo ra trong quá trình vẽ, đặc biệt là đối với các loại thép hợp kim làm cứng.
- Vẽ là một quá trình lâu dài. Có rất ít tiềm năng để điều chỉnh sự biến đổi thành dọc nghiêm trọng bởi vì khuôn và trục gá là nổi tự do và sẽ tuân theo sự biến đổi của thành thay vì sửa nó.
Bản vẽ nguội có thể được tối ưu hóa bằng cách chọn cấu hình khuôn phù hợp nhất (Xem Nhân vật 3). Không có thiết kế duy nhất nào hoạt động tốt nhất cho tất cả các ống liền mạch vì thiết kế phụ thuộc vào nhiều yếu tố, chẳng hạn như độ dày của tường, lớp thép, vượt qua yêu cầu giảm, và rút ra những hạn chế của băng ghế dự bị.
Nhân vật 3
Ba cấu hình khuôn bế bản vẽ nguội chính là bán kính, dài, và pha trộn thẳng / bán kính, hoặc kết hợp
Ba hồ sơ chết là:
- Bán kính khuôn — đầu vào khuôn là một vòng cung không có góc nhọn hoặc bề mặt phẳng.
- Khuôn thẳng — đầu vào khuôn có một mặt phẳng, bề mặt góc cạnh, thường 10 đến 20 độ mỗi bên.
- Khuôn kết hợp — đầu vào khuôn kết hợp các bề mặt phẳng và hỗn hợp bán kính.
Đối với mỗi đơn đặt hàng sản xuất được rút ra, một biểu đồ kiểm soát thống kê hoặc phương pháp kiểm tra t Student có thể được hoàn thành và được sử dụng để tối ưu hóa cấu hình khuôn và kích thước khuôn như một bản ghi vĩnh viễn.
Đối với hầu hết các ống liền mạch, khuôn bán kính tạo ra chất lượng tường tốt nhất. Bởi vì khuôn bán kính có biên dạng đầu vào dần dần và hòa trộn mịn vào phần ổ trục, rút ống nhất quán hơn và dẫn đến kích thước chất lượng cao hơn. Nhưng có một nhược điểm của loại khuôn này: Vì hồ sơ đầu vào dần dần, chỉ có thể giảm OD nhỏ trên ống. Ống liền mạch phải được tùy chỉnh để sử dụng loại khuôn này, thêm chi phí chuyển đổi.
Đạt được tính nhất quán một cách nhất quán
Để đạt được tính nhất quán đòi hỏi phải phân tích ngược quá trình, từ cuối đến đầu. Độ dày thành phẩm do khách hàng chỉ định cung cấp kích thước cuối cùng cho ống được xử lý bởi bàn ghép, hướng dẫn nào chết và lựa chọn trục gá. Lựa chọn này xác định kích thước ống phù hợp từ máy nghiền liền mạch, xác định các thông số thiết lập và vận hành thích hợp.