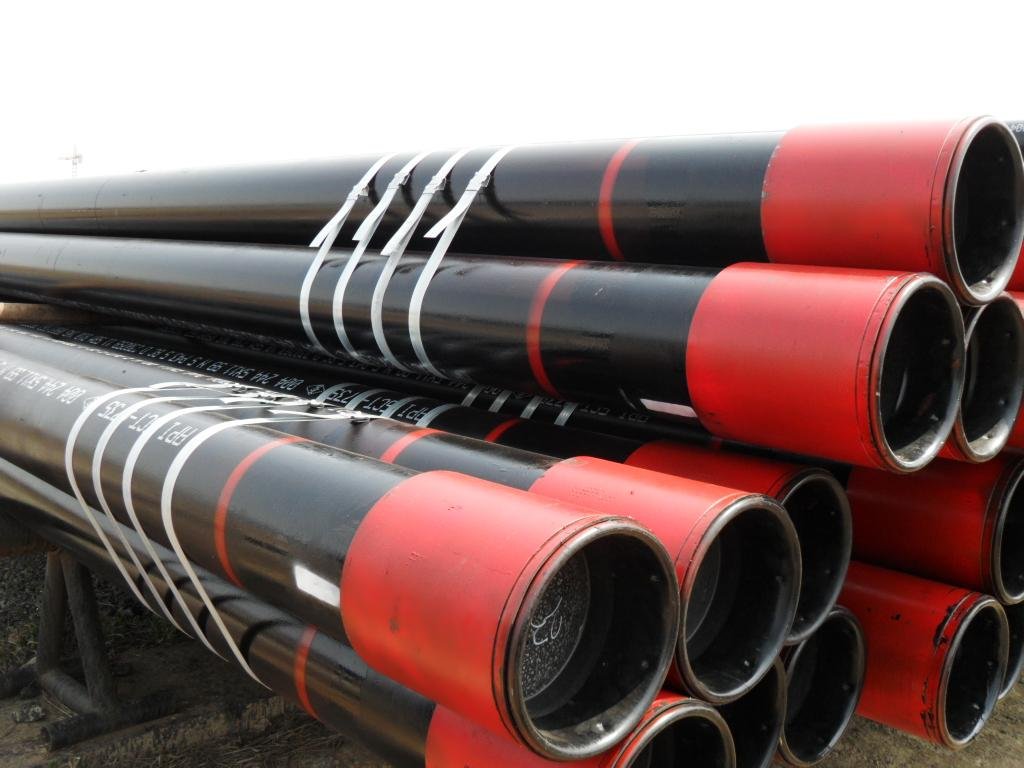
Performing Casing and Tubing Design
December 30, 2017Bearing Pile, welded pipe Piles for construction
January 8, 2018 Introduction
Well screens are a crucial component in water wells used to extract groundwater while preventing the passage of formation sediments into the wellbore. Over decades, stainless steel wedge wire screens have proven highly effective and durable for this purpose. In this report, I will provide a comprehensive overview of wedge wire screen design, analytical discussion of 304 stainless steel as the preferred construction material, comparisons with alternative screen types, and considerations for proper specification and installation. The aim is to impart a thorough technical understanding of these vital well components to engineers, hydrogeologists and contractors.
1. Slot size(mm): 0.01~3mm
2. Open area: up to 60%
3. Material: low carbon, low carbon galvanized steel (LCG) steel treated with anticorrosion coating, stainless steel (304, 316L etc)
4. Unit Length up to 6 meters
5. Diameter: ranging from 25 to 800mm
6. End connection: plain beveled ends for butt welding or threaded coupling or flange.
Screen Size | Inner Diameter | Outer Diameter | OD of Female Threaded End | ||||
in | mm | in | mm | in | mm | in | mm |
2 | 51 | 2 | 51 | 25/8 | 67 | 23/4 | 70 |
3 | 76 | 3 | 76 | 35/8 | 92 | 33/4 | 95 |
4 | 102 | 4 | 102 | 45/8 | 117 | 43/4 | 121 |
5 | 127 | 5 | 127 | 55/8 | 143 | 53/4 | 146 |
6 | 152 | 6 | 152 | 65/8 | 168 | 7 | 178 |
8 | 203 | 8 | 203 | 85/8 | 219 | 91/4 | 235 |
10 | 254 | 10 | 254 | 103/4 | 273 | 113/8 | 289 |
12 | 305 | 12 | 305 | 123/4 | 324 | 133/8 | 340 |
14 | 356 | 13 1/8 | 333 | 14 | 356 | —- | —- |
16 | 406 | 15 | 381 | 16 | 406 | —- | —- |
20 | 508 | 18 3/4 | 476 | 20 | 508 | —- | —- |
Profile Wire | ||||||||
Width (mm) | 1.5 | 1.5 | 2.3 | 2.3 | 1.8 | 3.0 | 3.7 | 3.3 |
Height
(mm) |
2.2 | 2.5 | 2.7 | 3.6 | 4.3 | 4.7 | 5.6 | 6.3 |
Support Wire | ![]() |
![]() |
![]() |
![]() |
![]() |
Round Wire ● |
Width(mm) | 2.3 | 2.3 | 3.0 | 3.7 | 3.3 | Ø2.5mm-Ø5mm |
Height (mm) | 2.7 | 3.6 | 4.7 | 5.6 | 6.3 |
Design and Construction
Wedge wire screens derive their name from the wedge-shaped wires wrapped helically around a cylindrical base pipe or blank ( usually Schedule 80 PVC or carbon steel) to form continuous slots ( ASTM D5978, 2014). Slot sizes range from 20 to 200 microns depending on the grain size distribution of target aquifers. This achieves a high open area ratio around 60-70%, maximizing inflow while excluding finer particles. Importantly, the wedged configuration allows for self-cleaning as the gaps adjust during development/pumping preventing clogging. Screens are available pre-assembled or for field wrapping in various diameters up to 24 inches and lengths. Quality control ensures uniform slot sizing and hydraulic efficiency.
Material Selection – Stainless Steel
Stainless steel, specifically type 304, has emerged as the premier material for wedge wire screens due to balanced mechanical strength and corrosion resistance properties vital for well longevity (American Society of Mechanical Engineers, 2019). Its 18% chromium content forms a protective passive oxide layer resistant to groundwater chemistries and microbiologically influenced corrosion which plague carbon steel and coated alternatives over time. Galvanic corrosion is also non-existent when paired with common PVC or FRP casing. Furthermore, stainless brings superior ductility allowing for easy slot forming during manufacturing while retaining yield strength through the screened interval. Recent field studies confirm minimal rates of degradation after 30+ years in-ground (Smith, 2018).
Competitive Screen Types
Continuous slot screens offer high intake but are prone to plugging without self-cleaning abilities. Plastic screens suffer from UV degradation if exposed. Pre-packed gravel packs require additional installation steps and costs. Stainless wire-wrapped screens provide openings comparable to slot sizes but not the robustness of wedge wire design. Similarly, fiberglass wrapped screens lack the conductivity of metal and mechanical strength. Thus, stainless steel wedge wire has emerged as the first choice for long-term, dependable groundwater intake (Bradley, 2016). Engineering criteria and site conditions will still dictate the optimal screen selection in certain applications.
Specification Factors
Key factors for engineers specifying wedge wire screens include: intake capacity needs, aquifer grain size distribution, conformance with ASTM/NSF standards, length and diameter sizing, connection to casing/riser pipe, filter pack gradation/thickness and annular seal methods. Hydraulic conductivity tests help ensure specified slot sizes achieve design yield. Stainless material, quality coating/wraps, and certification from reputable manufacturers also impact long term performance and code compliance. Value engineering is prudent to balance capital with operation/maintenance costs over a well’s design life.
Installation Considerations
Proper placement and development is needed to realize the full service life of wedge wire screens. They should be positioned at target water bearing intervals to avoid drawing unwanted fines. A graded filter pack supplemented with a 2-5% swell bentonite seal above/below protects the well and isolates zones. Development methods activate the self-cleaning property by surging/bailing to settle-in filter media. Post-installation testing ensures design goals for intake capacity and water quality are achieved before being placed into long-term operation. Following best practices during construction prevents early failures.
Field Case Studies
Extensive case studies from water utilities and state/provincial monitoring programs showcase the excellent, long-lasting service provided by stainless steel wedge wire screens decades after installation (Water Research Foundation, 2020). For example, rehabilitation video of a 70 foot screen section installed in 1963 showed little to no corrosion or plugging after 57 years of constant pumping in a brackish coastal aquifer. This performance provides compelling evidence for the longevity and reliability inherent to these designs when properly specified and placed in suitable conditions.
What are the advantages of using stainless steel wedge wire screens compared to other screen types?
There are several key advantages of using stainless steel wedge wire screens compared to other screen types:
Self-cleaning ability – The wedged wire design allows solids to pass through without getting stuck, reducing risk of clogging over time. This is a major benefit versus continuous slot screens.
Higher intake capacity – At 60-70% open area, wedge wire screens have greater intake potential than wrapped or slotted screens thanks to their efficient open-area configuration. This maximizes well yield.
Durability – Stainless steel construction makes wedge wire very resistant to corrosion and impacts and the life expectancy exceeds 50+ years based on case studies. Most other materials like plastic will degrade faster.